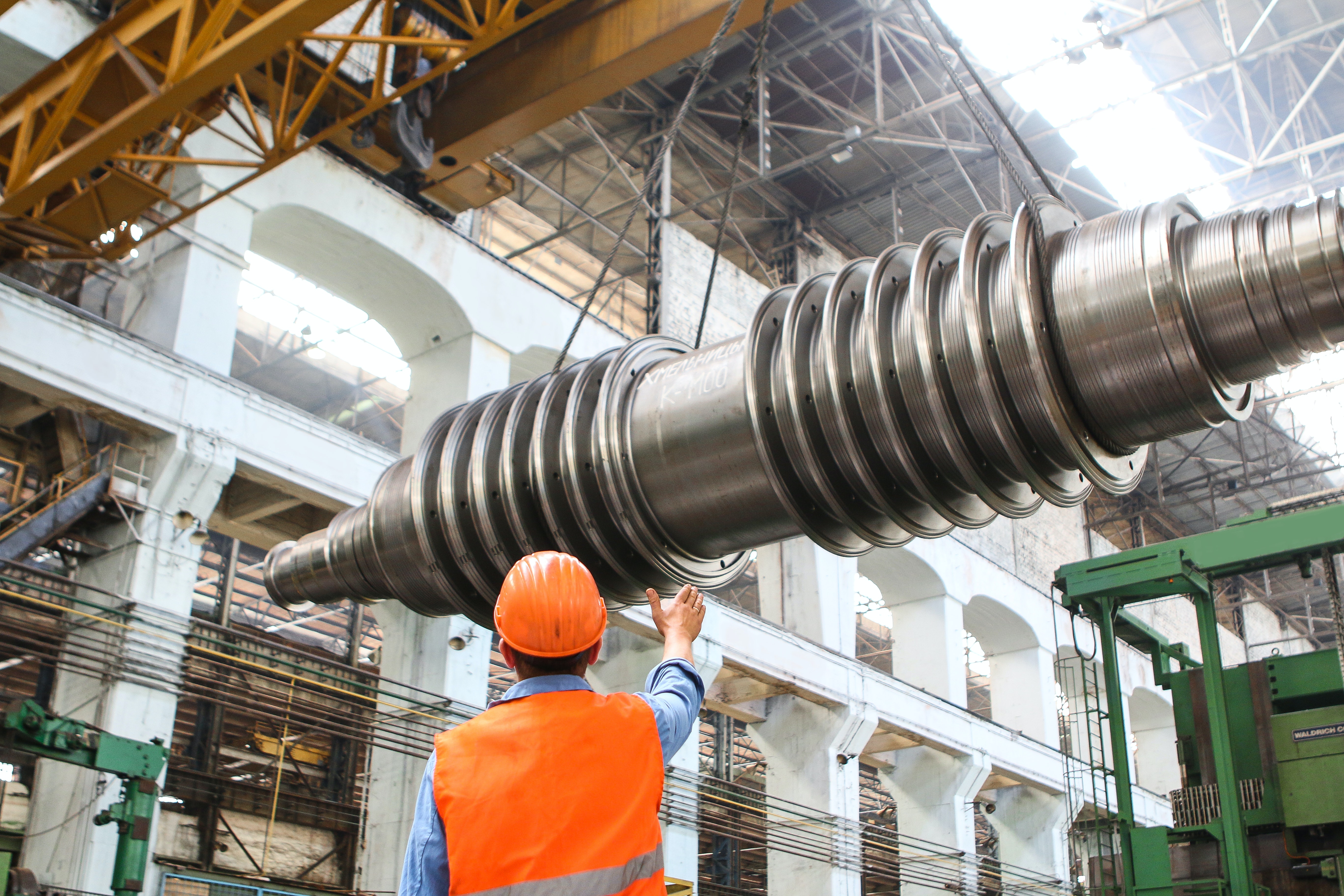
Types of quality control inspections
Instead of waiting for something to go wrong and reacting, businesses can proactively book quality control inspections to ensure they don’t run into these costly problems.
Ensuring that products are being sourced ethically and under positive working conditions is a major challenge in the global market. Social monitoring systems exist to track companies’ practices and help buyers make important decisions. The BSCI is one such methodology for social auditing and reporting for making improvements.
The Business Supply Chain Initiative (BSCI) is a tool established in 2003 that companies use to help make working conditions along their supply chain better. Its focus is on international conventions for workers’ rights, and businesses that take part in BSCI should enact a common code of conduct to help ensure these moral business practices.
BSCI was originally developed by the non-profit Amfori (previously known as the Foreign Trade Association) and has two tiers of membership: “Regular” companies that actively implement the BSCI process into their supply chain and “Associate” companies that support the effort but don’t implement BSCI. Businesses that do implement the process agree to follow these 11 principles:
Participating in the BSCI process can lead to several benefits. First and foremost, it helps ensure workers are able to complete their tasks in humane and ethical conditions. Following an ethical code also helps gain customers’ trust and improve the business’s brand.
Breakdowns in efficiency and the ability to meet industry standards are often caused by unknown or nebulous requirements. The BSCI process itself outlines very clear expectations for best practices on social performance to ensure participating companies meet standards on a consistent and satisfactory basis.
The BSCI report is the outcome of a BSCI audit. A supplier being audited will first consent to the audit and receive an audit plan. Audits may be unannounced, scheduled at a specific time, or arranged within an approximate time frame but not on an exact date.
When an audit begins, an opening meeting will be held to detail the process and goals of the inspection. Auditors may inspect the manufacturing floor and conduct interviews with employees, including management. The audit may include obtaining photographs or requesting and reviewing other forms of documentation from suppliers. Documentation can include procedures, company policies, and health and safety products. Auditors will use this information to determine how well a supplier is implementing the BSCI code of conduct and record any deficiencies or successes in a BSCI report.
A BSCI factory is simply a manufacturer that is a BSCI member. If they are regular members, they incorporate BSCI auditing into their structure. Audits that receive high ratings are valid for two years. These audits aim to help BSCI factories gradually and continually improve the social conditions in their business supply chain.
No matter the industry, verifying your company’s ability to meet social and ethical guidelines is good business sense. Book a demo to find out how Factored Quality’s network of inspectors can help your facilities meet today’s standards.