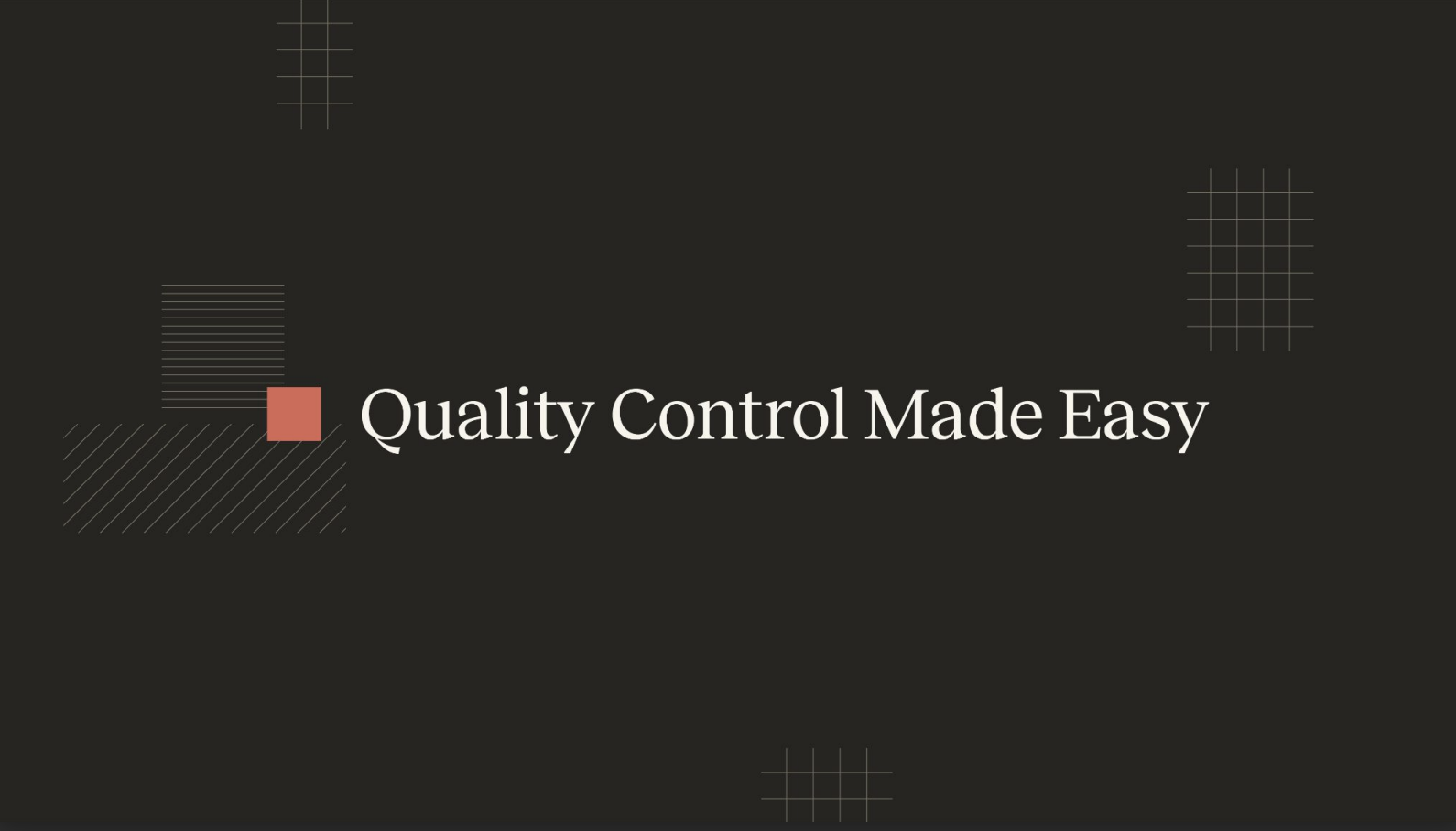
Founding Factored Quality: from NASA’s labs to leading QC platform
The best products come from teams who’ve experienced the problems they’re solving first-hand. Factored Quality is no exception.
Quality control is a process that is used to ensure that the quality of a product or service meets the customer's expectations. It is important to implement quality control in your business in order to maintain high standards and keep your customers happy. In this blog post, we will discuss what quality control is, why it is important, and how you can implement and improve it in your business.
Quality control is a process that checks whether the quality of a product or service meets expectations.
It is important to have quality control in order to:
In addition, quality control is important because inconsistent product quality can lead to costly mistakes and lost customers. If a shipment comes back with product errors, not only is the product now defective, but this typically costs many months of time to receive a new shipment of product.
There are two main types of quality control:
Prevention or Pre-Production QC: This type of quality control focuses on preventing mistakes from happening in the first place. Pre-production quality control checks whether the products or services meet the quality requirements before they are produced.
Post-Production QC: This type of quality control checks for mistakes after the product or service has been produced. Post-production quality control checks whether the products or services meet the quality requirements after they have been produced.
There are a few steps you can take to implement quality control in your business:
There are a few ways you can improve quality control in your business:
Quality control is an important part of any business. By setting quality control standards, investing in quality control tools, and encouraging employees to report quality problems, you can help improve quality control in your business.
Do you have additional questions about your quality control process? Reach out to speak with a QC specialist!