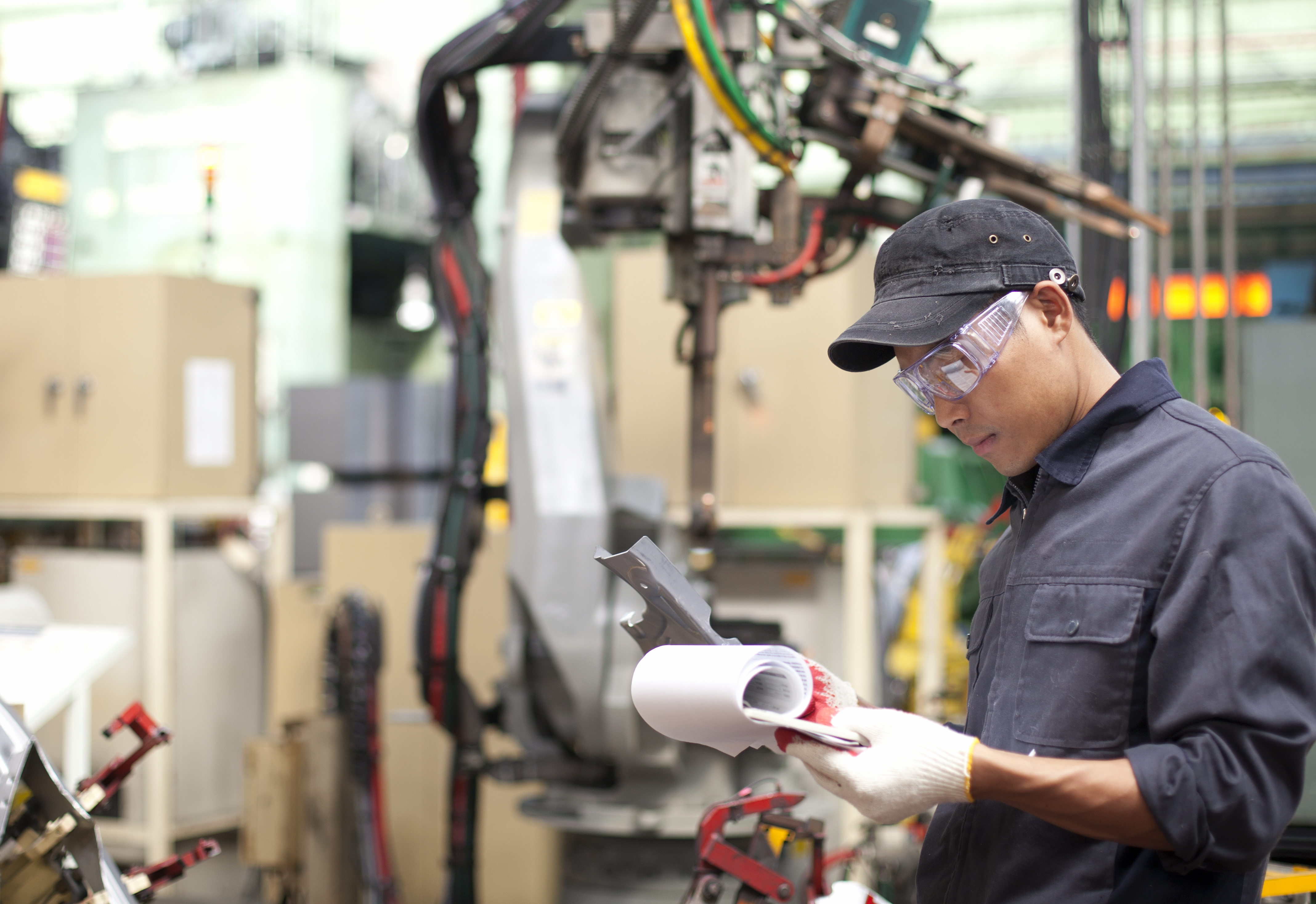
The Factored Quality Guide to RCAs & CAPAs
In Part 5, we unpack the ins and outs of RCAs and CAPAs.
In Part 4, we take a deep dive into warehouses: both inventory audits and counts.
Any consumer brand will know navigating from product development to warehouse inventory audits is a highly specific process.
Fortunately, at Factored Quality, we’re experts on all aspects of audits that founders and startup operations teams don’t have the capacity to worry about. And we’re going to outline all of them in this series.
In Part 4, we unpack warehouses: both inventory audits and inventory counts.
Let’s dive in.
Let's start with some definitions.
While you've (hopefully) already performed in-line inspections and pre-shipment inspections, brands often audit the inventory after they receive it to screen for additional customer complaints.
For example, one Factored Quality client received reports of an issue with their baby care products. To ensure they didn't sell any more faulty goods, they audited every unit in their warehouses.
With this, here are three reasons why inventory audits and counts are worthwhile investments:
Founders occasionally ask us why inventory counts are still necessary when warehouses supposedly have management systems with up-to-date, automatic counts.
Unfortunately, through countless clients and our team’s collective years in supply chain and QC operations, we know this is rarely the case. Elevated, automated warehouses may have that technology — but most warehouses that service SMBs do not, hence the need to invest in inventory counts for true visibility into what’s in your warehouse(s).
Inventory counts are necessary to build out accurate financial statements like business scales and quarterly reporting, which are then used to raise additional funds and provide shareholder reviews.
Inventory audits can directly improve and protect your customer experience and brand reputation.
You can design beautiful packaging — but, at the end of the day, if the product fails to function or look as promised, you’ll get a disappointed customer. All of the time and funds poured into that product will be a waste.
The only surefire way to satisfy customers is a brilliant, high-quality product — every single time. As such, audits keep production execution on par with your designs and intentions.
Here’s one IRL example of how audits saved the day for a Factored Quality client’s products:
With this information, the brand was able to make the correct inventory decisions, maintain customer satisfaction with the end products, and even price units accordingly.
Or, when partnering with another brand, FQ audited a facility producing medical-grade products — and discovered the supplier did not take necessary safety precautions while handling each unit. Any kind of issue with medical-grade products can pose serious risks to the end user. Luckily, we alerted the brand, who worked with the supplier to initiate a new quality assurance program.
Your products do not live in a void. Most commonly, they can be affected during shipping. As such, if you receive reports of damaged goods from customers, inventory audits are a reliable way to figure out where that damage is occurring.
For instance, if your pre-shipment inspections come back clean, you know the damage is likely occurring between the supplier and the warehouse or after the product leaves the warehouse.
Beyond this, here’s a glimpse at how Factored Quality expertly investigates defects:
When the FQ team runs product inspections, we start by giving clients scores on their factory and supplier audits.
With that audit score, we take one of three courses of action:
This data allows our client to return to their supplier with clear directions for fixing the product.
Once we come up with a solution, it is crucial to ensure it’s properly put in place — whether that’s at the manufacturing facility, the warehouse, etc.
For instance, our client can bring us in to conduct a First Article Inspection, where FQ critically inspects several units of the new product and compares it to the original design as soon as it comes off of the line.