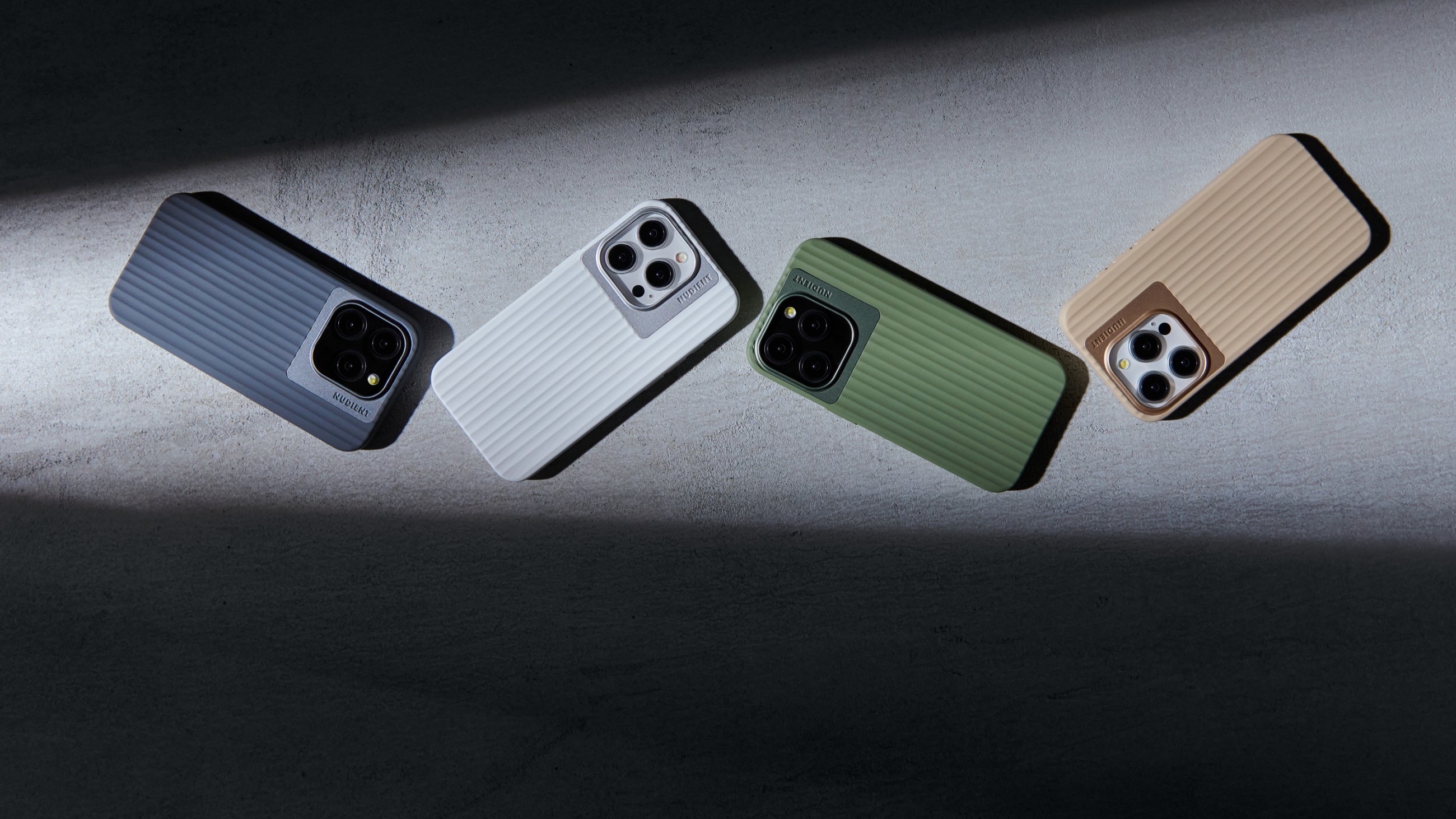
How Nudient reduced quality issues by 25% with Factored Quality
Learn how Nudient redefined its approach to quality control, leading to valuable time savings and greater confidence in large-volume orders.
“I showed a few investors the FQ dashboard, and they were shocked. They didn’t know you could monitor quality with this much detail, let alone easily share it. I fear we have set the bar high for their other investment companies — unless they’re on Factored Quality.”
Since 2015, Misen has made high-quality cookware more affordable for every kitchen, carefully researching and selecting top-end materials for all their products. Their products range from premium kitchen knives and cookware to essential utensils, all designed to make prepping and cooking easier.
Misen's commitment to delivering quality cookware required a more centralized and less reactive approach to product defects. Quality issues could go unseen or pop up at any moment, and they needed to track changes in quality over time. While these audits provided valuable insights, they only spotted defects after they occurred.
They tried working with third-party providers to run quality checks, but the processes were all different and coordinated by a 3rd party agent, making communication difficult and extending the time to solve. Misen urgently needed a centralized, hands-off solution that could offer real-time insights into quality metrics, allowing them to make QC decisions based on product data.
“We needed to look into bigger, deeper, and better solutions because quality needs to be tracked like any KPI.”
With the help of Factored Quality's comprehensive platform, Misen can now go beyond individual audits. FQ's unified dashboard brings together the QC data from every inspection and product test to generate reports tracking the evolution of quality over time.
Now, Misen's team can analyze the trends to spot new ways to improve their quality control practices and spread the information throughout the company. By equipping every employee with this understanding of the trends, Misen ensures that their team is alerted to any potential quality gaps so any issues can be resolved preemptively.
FQ also helps Misen find the right inspectors and auditors to ensure the QC data is accurate and timely. These certified partners cover every quality control and compliance step, freeing up bandwidth for Misen's team. Instead, they can focus on designing and developing new products, trusting the platform and process to identify potential product issues - before they become real.
Unlike Misen’s previous QC process, their team isn’t left to navigate quality issues on their own. FQ’s experts are eager to understand Misen’s production concerns and offer support at a moment’s notice.
“It would have been pure hubris to think we could create a great quality program on our own. With Factored Quality, every time we've asked, ‘Hey, we need something,’ they say, ‘Here's what you really need.’ Leveraging a partner that supplies strategy as well as people and technology has been a big win for us.”
Since implementing FQ, Misen can see and address quality concerns earlier in the manufacturing process. With their new QC partners handling the inspections and audits, Misen’s team has the time to be more proactive with their quality control.
Misen’s stronger quality process has led to impressive results:
By embracing proactive QC management, Misen stands poised for continued success in a competitive, quality-driven marketplace.
“With FQ, our defect rates at every step of manufacturing have improved and our revenue forecast would probably be lower without their support. That’s the holy grail of quality.”