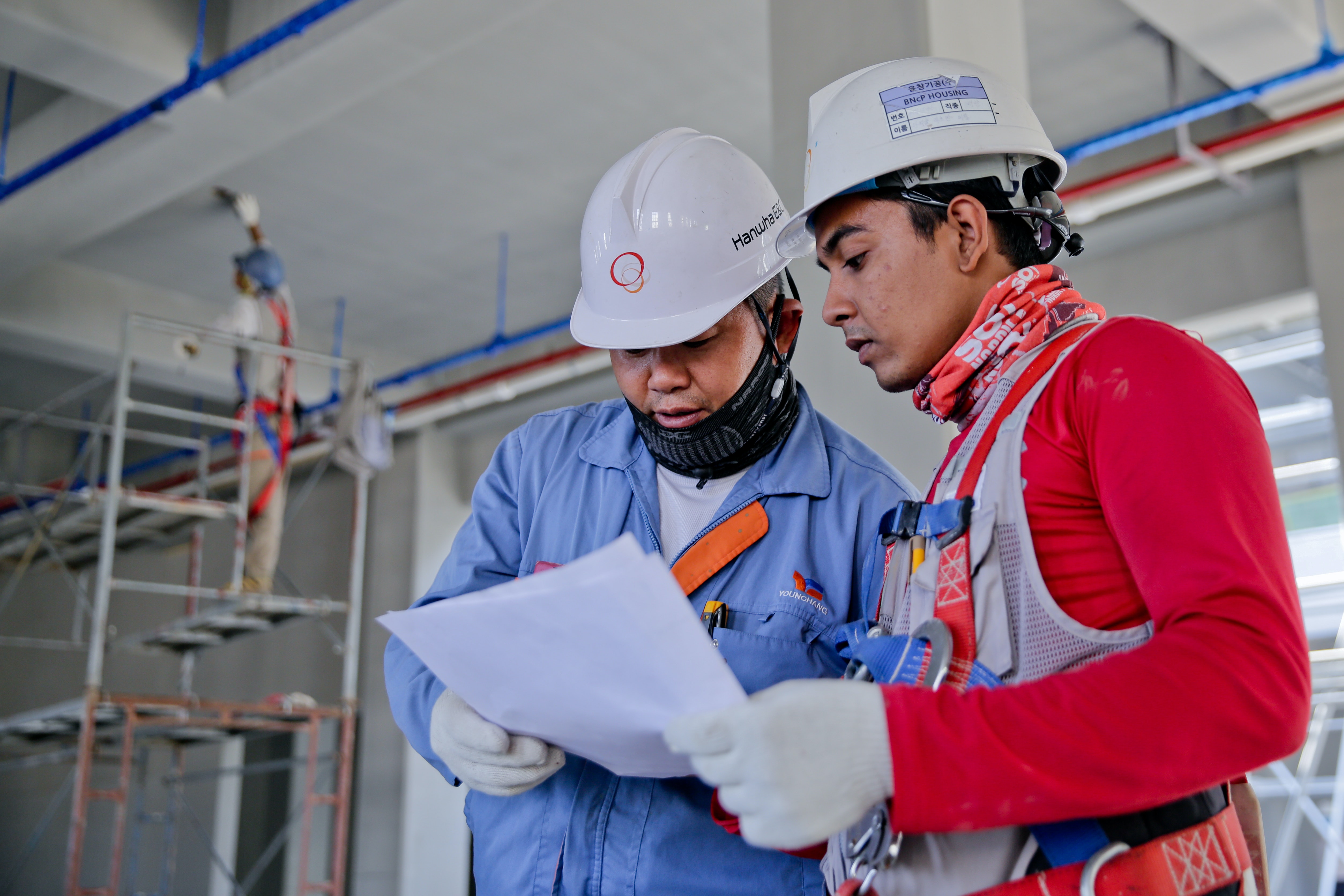
A guide to product quality testing
Setting a standard and making sure every product meets that standard and is made ethically builds consumer trust and loyalty.
Making quality products is about more than one great batch. Every component and design aspect needs to meet strict specifications within each batch and between runs to ensure consistency. Quality control inspections are designed to help your products conform to company, industry, and government standards, whether you’re producing components for future assembly or finished items.
The short answer is that a quality control inspection is a way to make sure your end product meets expectations. It’s an opportunity to identify shortcomings so they can be corrected. These standards can be defined in the design, such as size and tolerances for its dimensions, durability, and appearance. They may also be set forth by government regulators and other industry standards. For example, medical devices often have specifications for ensuring uniformity and safety.
QC inspections are done by trained professionals who have experience providing quality control services for similar products. These individuals are ideally familiar with related industry standards. Before conducting an inspection, they’ll also become familiar with any additional expectations.
This information is combined into a quality control checklist they can then use to verify their tests, measurements, and visual inspections against. In addition to this golden standard, they’ll know the lowest allowable quality. After the inspection is complete, the inspector will provide a report with their findings so any issues can be remediated.
To conduct a quality control inspection, the servicer will utilize a QC checklist that outlines specifications to check and test the product against. QC checklists cover product requirements, such as dimensions of the final product or its components, color and appearance, paint finish, and material make-up. It can also include requirements for packaging, such as labeling, warnings, weight, and imagery.
The list may have testing requirements ranging from electrical standards and shielding to waterproofing and durability. Collaborating with suppliers and manufacturers to create a QC checklist ensures there are clear expectations and that everyone understands what standards the product needs to meet.
If you want to keep your focus on innovation, let Factored Quality worry about quality control. We’ll ensure your product is up to your customers’ expectations with in-line inspections, pre-shipment inspections, and factory audits. Witness how Factored Quality can help you reduce unnecessary costs by signing up for a product demo today.