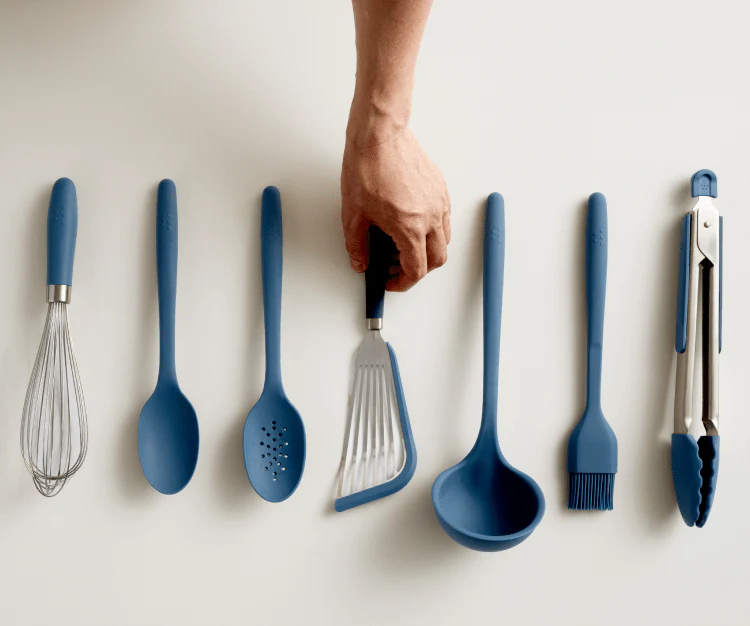
How Misen decreased product defects by 75% with FQ
Learn how Misen improved product quality across the board with Factored Quality's unified platform and QC services.
“The Factored Quality team is quick, their platform is easy to use, and their communication and service quality are great. With FQ, I can refocus on managing operations because I trust them to handle quality control. That’s why we’ve partnered with them.”
Called “the most thoughtfully designed sneakers ever” by Vogue, Atoms is the Brooklyn-based footwear brand known for their simplistic style you can wear anywhere. Atoms are also the only major sneaker on the market that comes in 1/4 sizes. Founded in 2018, the brand’s tech-first ops made them the perfect fit for Factored Quality’s centralized quality control offerings.
As a lean startup and a DTC brand, the Atoms team faced an unfortunately common dilemma: Skyrocketing sales and business opportunities are exhilarating. However, workflows like quality control can fall by the wayside when your team is stretched too thin. Atoms enlisted a third-party QC vendor to try to address this — but soon realized this was not enough.
According to Yechan Yoo, Head of Product Operations (Asia) at Atoms, they saw social media posts and customer reviews with complaints about sneaker quality. These were a major red flag for two reasons:
To address this ASAP, Yechan knew his small, scrappy team needed a third party they could trust. That’s when Factored Quality stepped in.
“After hearing from customers that we were having quality control issues, we needed a reliable partner to check shipments on our behalf. We knew FQ would be the best candidate for that.”
When Yechan reached out to Factored Quality, we were immediately prepared to onboard Atoms, dive into their production chain, and help revamp their QC. This happened in three key steps:
Atoms equipped FQ with their product quality guidelines so we could get up to speed on their existing shoe standards. Our team of supply chain and QC experts collaborated with Yechan to identify any areas for improvement and continually iterate on it with customer feedback.
FQ facilitated an easy collaboration between Yechan’s ops team, Atoms’ manufacturing partner, and our network of over 2,000 trained, certified, and vetted inspectors worldwide. According to Yechan, the ability to hand over Atoms’ checklists to an inspector and fully trust that they would deliver was a key selling point of Factored Quality.
Yechan emphasizes FQ’s strict adherence to both our own internal standards and our clients’ standards for inspections. This shows in our technical platform’s thorough reporting and documentation of all inspection results. Yechan could easily log into his user portal to view results — complete with clear images and videos of the shoe shipments.
Since onboarding with Factored Quality, Yechan and his team have successfully solved customer quality concerns and freed up more time to refocus on operations.
Plus, because FQ plans inspections to happen before shipments leave the factory floor, Atoms will never waste cash to export another batch of faulty shoes. This literally pays dividends by saving on tariffs, shipping costs, and more, explains Yechan.
Take a closer look at the results Atoms has seen thanks to Factored Quality:
“I would meet with the inspectors, let them do their work, and then just get back to the office because they were reliable. From the beginning, Factored Quality was the only option for us because of how proactive and collaborative the team is.”