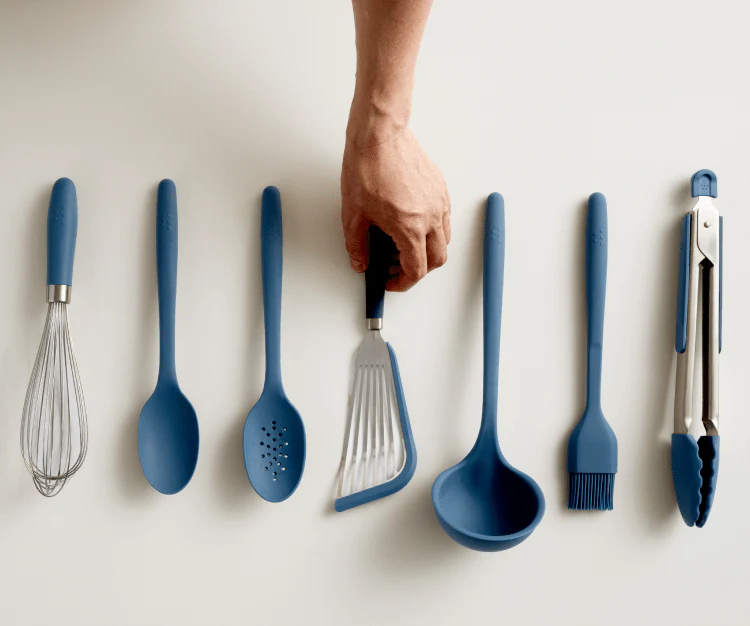
How Misen decreased product defects by 75% with FQ
Learn how Misen improved product quality across the board with Factored Quality's unified platform and QC services.
“When a customer invests in our products, they’re investing in us as a brand. All of our tools are warrantied for life, so we need to feel proud of what we send to customers. Factored Quality has made that seamless.”
Character is your next-gen, one-stop shop for all things home improvement — from curated toolsets to real-time troubleshooting from professionals. The brand prides itself on hardware products that are well-made, effective, and beautiful enough to display. Mo Opland, Head of Operations & Supply Chain at Character, reached out to Factored Quality on day one of production to lock down their product quality. Today, they trust FQ to maintain airtight QC operations in factories around the world.
From day one, Character planned to offer a wide range of customizable products — a lofty goal for a young brand. While their design team was confident in the brand’s visual appeal, they knew aesthetics alone wouldn’t cut it. So, they preemptively reached out to Factored Quality to ensure their goods could meet the highest standards of quality and function.
Opportunities for quality improvement included:
“Factored Quality’s parameters took away all of the decisions you’re faced with early in the production process. It was so helpful to start with FQ’s expertise and customize from there based on our needs.”
Manufacturing will always be impacted by external factors. That’s why Character values the adaptability of Factored Quality’s team and services. So far, FQ has supported the brand’s ever-evolving needs through solutions like:
“We're really appreciative that we can flex and collaborate with Factored Quality on what we need as situations arise in real time.”
Since onboarding with Factored Quality over a year ago, Character has seen impressive results, including:
FQ ultimately benefits Character’s bottom line by driving both cost efficiency and new lines of revenue. Inspectors ensure every product shipment is up to snuff before it ever leaves the factory, which slashes excess freight fees (i.e. sending an overseas shipment, only to open it up and find defects). As a result, the team at Character has the confidence to expand to new markets. Even if they don’t touch a shipment going straight from the factory floor to their retail partners, Mo affirms:
“The Character team can be confident in the quality of our product offerings thanks to Factored Quality.”
Looking forward, Character will be moving more of their production and assembly from their US warehouse to their factory partners in China. While that’s farther from home, Mo and her team can rest easy because they have Factored Quality behind them to ensure reliable quality control and find new ways to optimize their production processes for the long haul.
“Factored Quality has just always made the quality control process so easy. Working with them helps our brand build confidence in the fact that we’re sending the ideal product.”