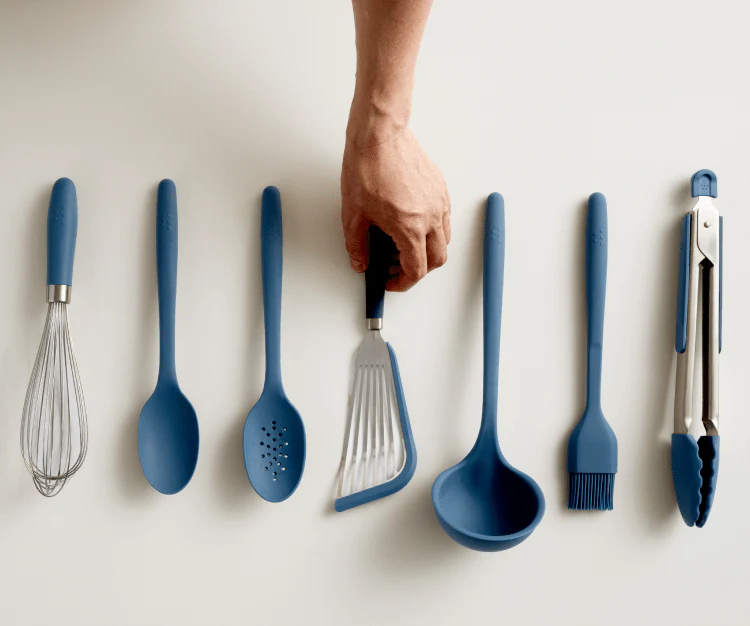
How Misen decreased product defects by 75% with FQ
Learn how Misen improved product quality across the board with Factored Quality's unified platform and QC services.
"We trust Factored Quality to come through 100% every single time. We're planning on using their other services to check the quality of the factory as we continue to grow. FQ gives us peace of mind & guaranteed quality."
Visp is the wellness company behind the first-of-its-kind, patent-pending Elixir Mixer. The innovative design whisks up your protein shakes, green juice, lattes, and more in 15 seconds. With Visp, you have a built-in barista making your daily routine feel effortless.
Mariana Kanellos and Harrison Alva, first-time Co-Founders of Visp, were dismayed to find that adequate quality control (QC) checks are not an automatic step in the factory production process. At one point, they even considered visiting the factory in China themselves.
Fortunately, other founders in the space and Visp’s design partners advised them to instead enlist a third party to inspect their products. So, the Visp co-founders began searching for partners — and soon discovered Factored Quality and decided to sign up.
After an easy onboarding flow, Factored Quality kicked off with our first pre-shipment inspection at Visp’s factory. The FQ team unfortunately found some serious workmanship missteps — but this incident immediately proved the value of the partnership to Visp. They dodged a serious bullet, and the factory has since addressed all sources of defects.
Since then, it has been easy for Visp to stage inspections across every production stage with FQ. Here’s a look into the end-to-end process:
Running your first international production order is difficult when so much capital is on the line. However, working with Factored Quality put the Visp team’s minds at ease.
"With the reporting, we know exactly what's in the boxes coming to our warehouse. It proves things were done correctly. There's a confidence knowing customers will receive that golden sample."
Since Visp is a luxury product, the brand cannot bear cosmetic errors, no matter how small. As such, FQ ensures customer satisfaction that matches the expectation of higher price point products.
Meeting that standard was critical, as Visp even delayed its launch to ensure product quality. They needed to see results — and working with FQ certainly delivered.
Take a look at some of the results FQ has enabled.
"If you sell a product for $88, there cannot be any defects. They're easy to find, but we wouldn't have found them early enough without Factored Quality. These minor mistakes would've made customers think less of our products."
Visp is amped to continue working with Factored Quality because, in Mariana's words, “FQ ensures that golden, perfect bottle 99% of the time.” Watching their product design vision consistently executed at such a high level is a relief.
Plus, whenever their team needs to troubleshoot or wants to try a new service, the people of FQ are just an email away. Visp feels like a truly supported, high-priority customer.
As for future products, the Visp team looks forward to asking FQ to evaluate new factories and suppliers to ensure they’re producing at the highest possible quality.